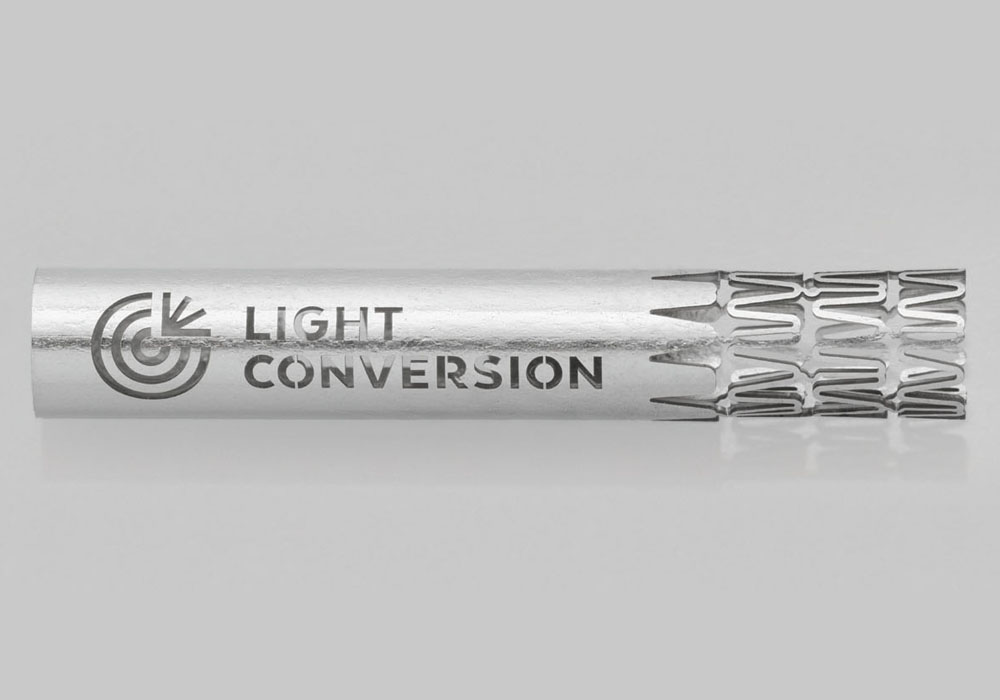
Medical Device Manufacturing
Laser micromachining for medical devices is driven by ever increasing demands in miniaturization and new functionalities required by the industry. Main processes include laser marking, drilling, cutting and welding of polymer and metal (steel, titanium, nitinol, etc.) components. Most medical devices need to be clearly and permanently marked for identification, traceability and advertising purposes. Laser cutting, drilling and welding of tubes or thin foils and films is often used for fabrication of various endoscopic devices including stents, implants, catheters, guide wires and other micro-components.
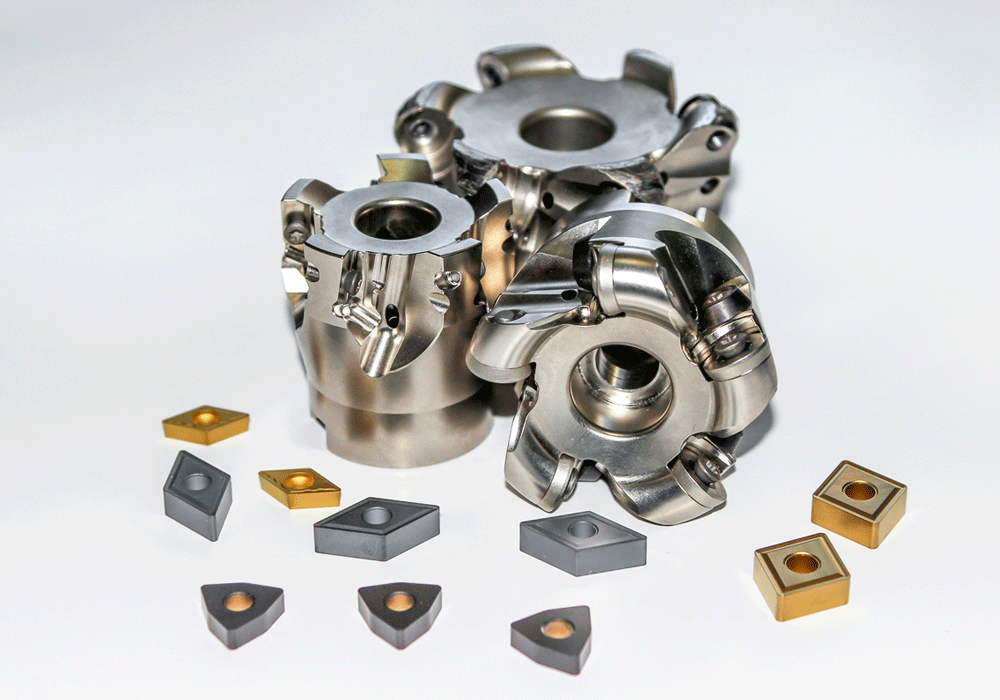
Tooling Industry
Most popular applications include permanent marking and engraving of various tools, tool holders, chip breakers etc. Ultrashort pulse lasers are opening new possibilities in PCD (polycrystalline diamond) tool shaping and sharpening. Laser processing enables processing of different materials, formation of complex 3D shapes and being a wear-free process makes quality control much simpler.
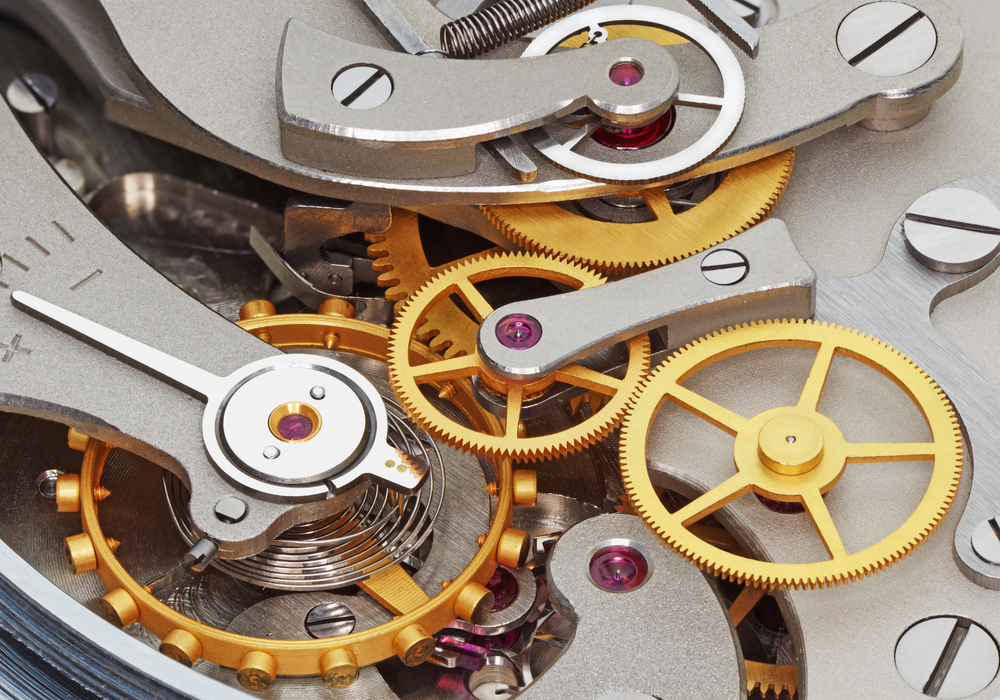
Watch and Jewelry Manufacturing
Typical applications include marking, engraving and surface texture formation for enhanced visual appeal, serial numbering or counterfeit purposes of various jewelry items and watch metallic or leather parts. More challenging applications include colored volume glass or sapphire watch windows marking and tapper-free metallic gear micro-cutting for mechanical watches.
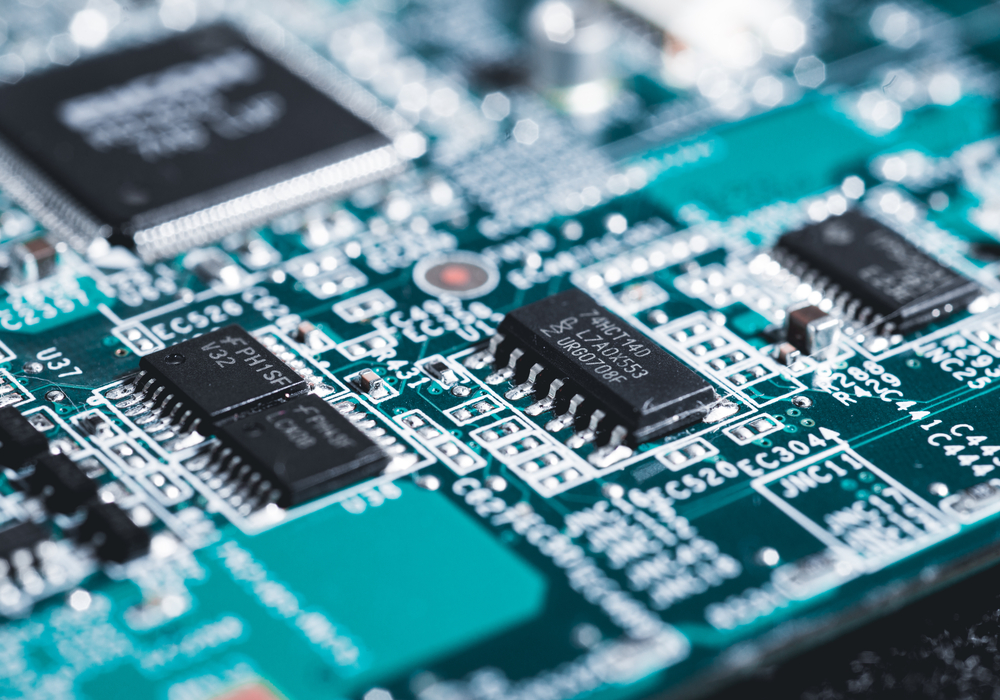
Electronic Components Manufacturing
Typical applications include marking and engraving of various electronic components including plastic coated or metal shielded ICs, metal lead frames, ceramic fuses, resistors, batteries, plastic connectors, various assembled electronic parts etc. Other laser processes include micro soldering, wire stripping, plastic welding, mold cleaning and more challenging ones like tuning of components with real time feedback.
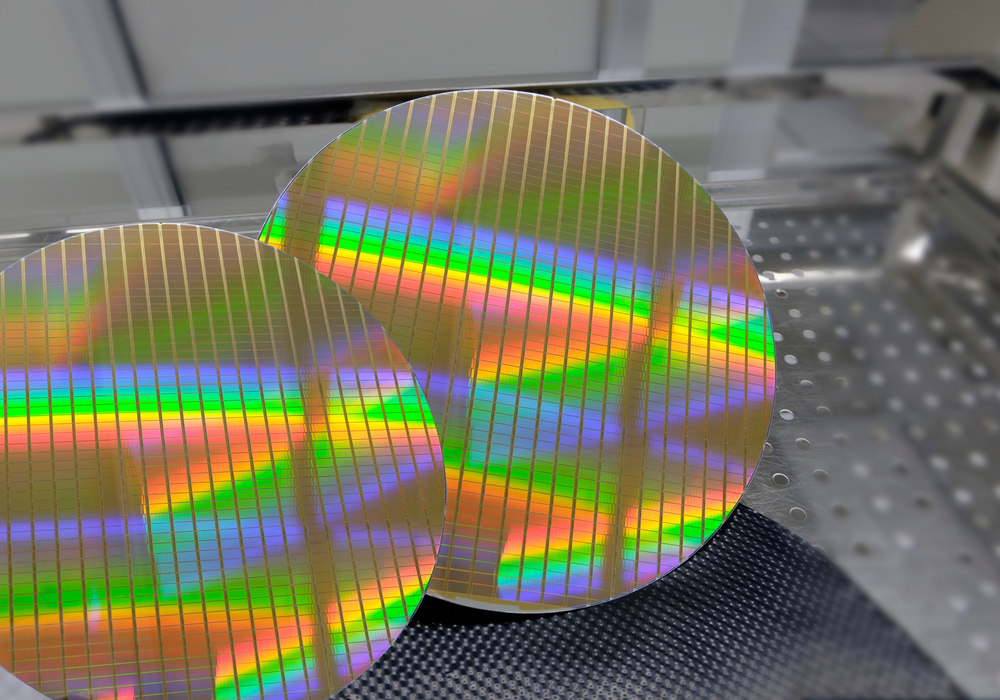
Semiconductor Industry
In the semiconductor industry lasers are often used for wafer separation into individual components. Wafers of different materials can be separated including silicon, sapphire, quartz, glass and others. Laser scribing is one of the most popular processes where a micron width groove is formed on one side of the wafer. For transparent materials, micron size defects can be formed through the whole thickness of the wafer which results in zero-width separation. In some processes metal coatings have to be removed which is also done by laser ablation. Glass drilling for wafer transfer is another application.
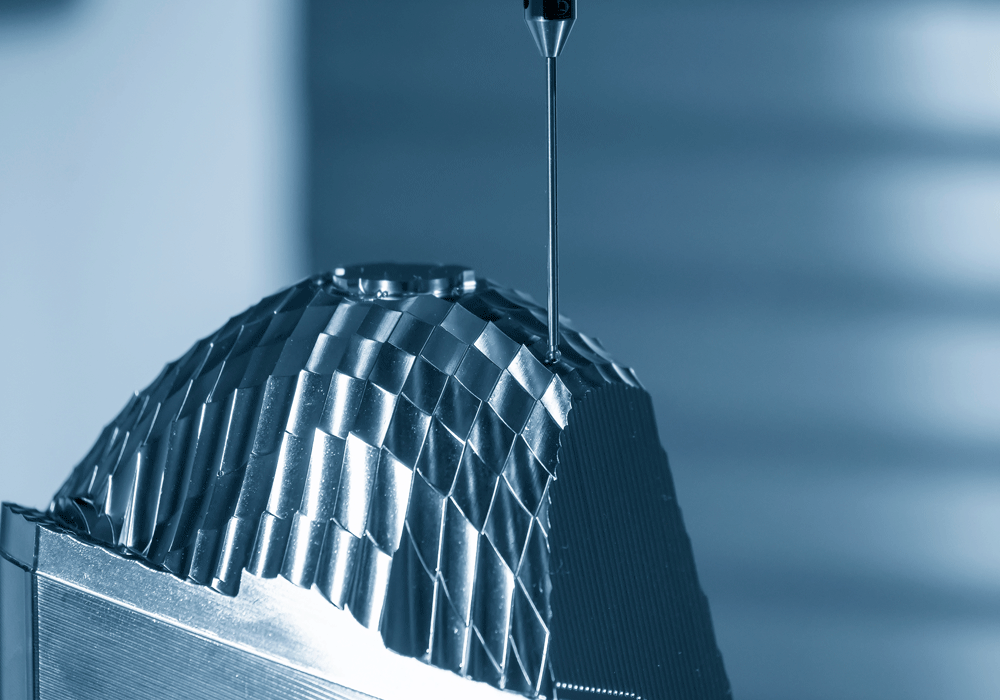
Automotive Industry
Deep engraving and surface texturing of molds, stamps and dies provides high flexibility in design and allows processing of hard-to-reach areas, surface texture control is used for better adhesion or improved esthetics of fabricated parts. High speed clean marking of various plastic, metallic or painted components, safe and permanent marking on technical ceramics e.g. spark plugs; fabricating background lighting buttons and many more. Ultrashort pulses enable high precision fuel injector hole drilling.